Because there are times when a business owner does not only have one or two types of goods, knowing how to handle an inventory system is vital for the efficient operation of a firm. The complete conversation may be found in this article.
It is common known that in order for their business to run successfully, business owners must provide a variety of things as stock or inventory. A suitable management system is required on a wide scale so that the stock can be continuously monitored.
This is referred to as an inventory system in business. In essence, inventory is stock.
So, an inventory system is a technique used by entrepreneurs to manage stock in their businesses. See the following reviews to gain a better understanding of the inventory and its connected issues.
Knowing Inventory
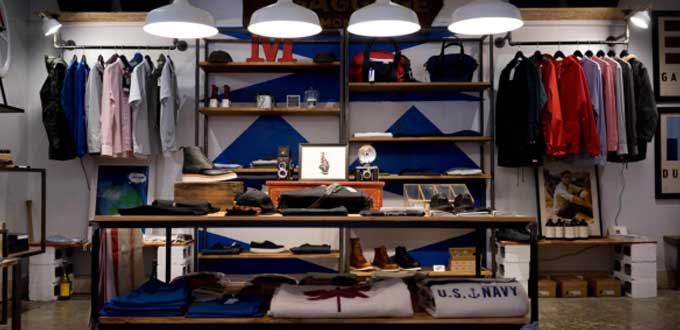
Although inventory terminology can be perceived as stock, the connotation can vary based on the industry. In general, inventory refers to any commodities or resources that a business owns and sells for a profit.
Inventory in the manufacturing industry might take the shape of finished goods that are ready to sell or raw materials and semi-finished goods that are held in warehouses.
In the meantime, in the service industry, inventory refers to the factors engaged in the process of purchasing and selling services.
An empty hotel room, customer and project information on consulting services, or documents and books to be translated by translation services are all examples of service business inventory.
Inventory Type
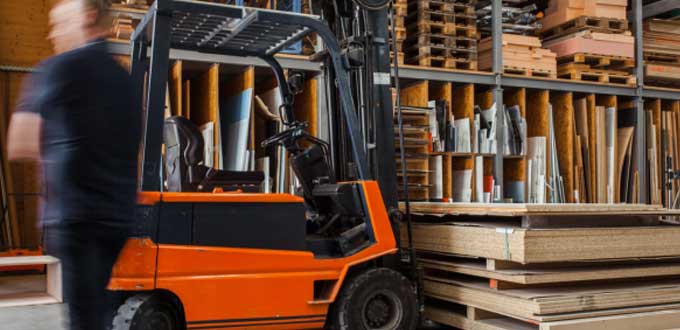
To better comprehend the inventory system, we must first understand the different forms of inventory so that we can manage it effectively.
1. the raw material
Raw materials are the first type of inventory. We cannot sell directly, yet we cannot produce outstanding business products without raw materials.
The term “raw materials” refers to all of the materials utilized to create the final product.
In the fruit juice beverage sector, for example, the basic ingredients are fruits and food sweeteners from diverse vendors.
These materials will be transformed into beverages in the future. These beverages will be sold and promoted. The concept of raw materials as inventory is typically found only in industrial plants.
Also read: What is Cost of Goods Sold?
2. Current Projects
Not only raw materials, but even labour done before the product is finalized, can be classified as inventory. For example, one sort of inventory in the process of creating fruit juice drinks is the process of extracting juice from fruits.
Not only does this apply to raw materials, but it also applies to finished commodities that are not yet ready for sale.
For example, cake items that have not been subjected to quality testing. Because it is still involved in ongoing projects or work, this cake product includes inventory.
3. Finished Products
Finished goods are typically defined as ready-to-sell products that will be distributed in the market. This product has passed all stages of manufacturing and quality testing. As previously stated, finished goods are included in the inventory category.
Finished goods are one of the most important inventories, and their existence is always recognized in the company’s financial accounts.
This is why finished goods are frequently engaged, and they have become a crucial component that should not be overlooked if the company does not want to lose money in the stock management system.
4. MRO inventory
MRO is an abbreviation for maintenance, repair, and operation. It is not considered inventory but plays a vital function in the firm.
MRO is typically utilized to perform maintenance and repair on machines or other tools used in the manufacturing process.
Engine lubricants, food coolers, uniforms, bolts, nuts, screws, and other goods are examples of MRO. This form of inventory is common in the industrial industry.
5. Assistance
Buffer inventory is a warehouse safety stock in the form of commodities to fulfill unforeseen needs or demands.
When a natural disaster strikes, there is a delay in the distribution of goods, or there is a strike, the presence of a buffer is quite beneficial.
Buffers are extremely useful for ensuring business continuity and maintaining consistent sales data. This is why the inventory buffer function is so critical. Furthermore, market circumstances are difficult to foresee and are always prone to unpredictability.
We conclude from reading evaluations about the various sorts of inventory that this plays a vital part in the industry. As a result, adequate management procedures are required.
How to Manage Inventory

Here are some pointers for managing a company’s inventory management.
1. Establish a priority.
There must be certain key forms of inventory among the numerous types of inventory discussed previously.
Determine stock priorities based on the categories that have been developed as a first step for maximum management. Put stock, for example, in the categories we order the most, rarely, and infrequently.
This category will assist us in managing finances so that the funds are properly managed. Waste can also be reduced so that the company’s financial situation remains stable.
Also read: How to Calculate the Selling Price
2. Keep track of all product details.
In addition to dividing the goods into different groups, make sure you document every piece of inventory information you have so that they can be tracked at any moment.
Fill in the blanks with information such as the barcode, lot number, supplier identity, or SKU (business certificate).
This stage can provide useful information that can be utilized to establish the selling price of goods in addition to tracking.
3. Conduct an inventory take audit.
Every industry must have a stock take that is always available.
Don’t be afraid to audit the inventory on a regular basis, whether it’s daily, weekly, monthly, or even yearly, to ensure that the stock system is always in good shape.
An audit can assist us in determining the correct number of available stock so that things that seldom sell will be reduced in stock or commodities that have a high level of interest will be added to enhance financial conditions.
4. Follow the 80-20 rule.
Ideally, 80 percent of income should come from 20% of things sold. In inventory management, strive to keep the 20% figure in mind.
Aside from being able to improve the company’s economy, this phase will assist us in understanding the sales cycle and determining which things generate the most profit.
As a result, ensure that there is an exact recap of the inventory system’s priority items.
In addition to some of the suggestions above, you may use software such as IREAP POS to assist you manage your inventory. IREAP POS runs a cashier application that may be used both online and offline and does accurate computations. The inventory system can be completed conveniently and practically with the help of this program.
That concludes the discussion of the inventory system and how to manage it. Based on these studies, it is possible to infer that the inventory system is an important component of firm management. could be beneficial.