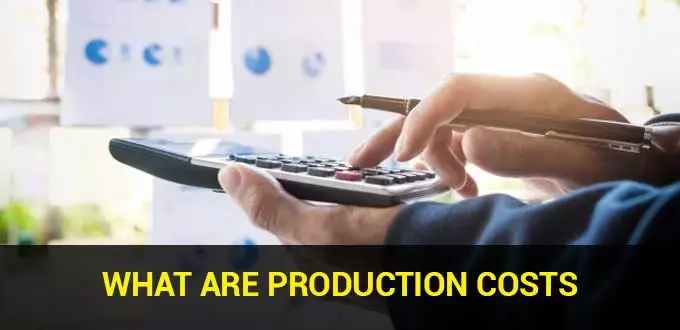
The meaning of Production Costs is the total costs that must be incurred or incurred by a company when carrying out the procurement process for both goods and services. Production costs can also be understood as the accumulation or calculation of production costs in the process of adding value to finished goods or services.
The calculation of production costs in a production or manufacturing business is very important, considering that this cost component is an important factor in determining the selling price. Errors in calculating production costs will cause wrong decisions and result in company losses.
Conversely, by calculating your production costs carefully, you can minimize unnecessary losses or expenses during production, and determine the right selling price.
Read also: How to Calculate the Selling Price of Your Product to Get Big Profits?
Functions and Purposes of Calculating Production Costs
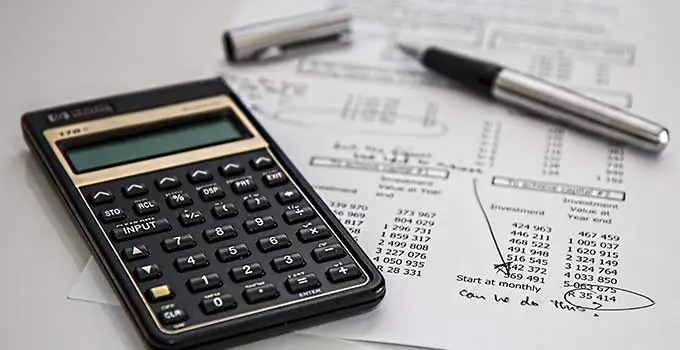
The following are some of the functions and purposes of calculating accurate production costs within your company:
1. Determining the right selling price.
By getting the right production costs or production costs, you can easily determine the selling price with the profit (margin) you want and are also acceptable to the customer.
2. Improve the quality of raw materials.
Production raw materials are generally the largest component in production costs. By understanding in detail the cost of raw materials, you can try to find ways to keep looking for better sources of raw materials, so that the goods produced are of higher quality and avoid production failures.
3. Improve the sourcing of raw materials.
Apart from looking for quality raw materials, you can also look for sources of raw materials from various suppliers. This is in order to get better and cheaper raw materials, which in turn reduces the production costs .
Read also: Functions and Roles of Producers, Distributors, Retailers, and Consumers in the Supply Chain
4. Efficiency in the production process.
Apart from raw materials, the second significant component is the use of resources. Neither human resources nor machines are used. This of course really depends on the type of goods you produce.
For example, a chemical or fertilizer factory will definitely have a higher cost of machine components than human resources, considering the production process must be automated. On the other hand, if you produce Garment, you will be very dependent on human resources that are higher than machine resources.
By understanding each cost in detail, you will be able to make efficient in every process that occurs.
Efficiency can be up to carrying out certain processes in production where other parties or suppliers can perform more efficiently. For example in Garment, it is common for companies to carry out the process of cutting materials but the sewing process is carried out by the supplier. This is commonly called the CMT (Cut, Make, Trim) process which different companies can do.
5. Assist management in decision making
By calculating the correct production costs , making decisions related to production costs includes purchasing raw materials, purchasing machines or production tools, and determining the selling price, and determining the profit that can be achieved by the company.
Components of Production Costs
1. Direct Material Costs
Direct raw materials are material costs that have a physical form and are identified as starting or raw materials that come into contact in a production process. This raw material will later be processed into a product that has an exchange value.
For example in a coffee shop, direct raw materials are coffee beans, milk, sugar, water, ice, and other materials that are directly used in the process of making coffee drinks. Other examples of bread factories are flour, eggs, milk, chocolate, cheese, butter, oil, and others.
2. Direct Labor Costs
Direct Labor Costs are costs paid to employees who are directly involved in the production process of goods.
Examples in coffee shops: wages, overtime, allowances, insurance for the barista who makes coffee. An example in a bakery is factory staff who carry out the production process every day, from making dough, baking to packaging finished goods.
3. Factory Overhead Cost (Factory Overhead)
Factory Overhead Costs are costs that are not directly related to the production process. Factory overhead costs consist of:
- Indirect Material
Indirect materials are materials used in the production process but tend to be difficult to allocate for each finished good.Example in a coffee shop: coffee maker cleaning liquid. In a bakery factory, oil for machines, soap, and cleaning water is produced every day.
- Indirect Labor
Indirect labor is employee labor who is not directly involved in the production process.Example in a coffee shop: security guards. In the bakery, the production administration section, supervisors, and quality control supervisors in the factory. All costs incurred to them will be classified as indirect labor costs.
- Other Overhead Costs
Overhead costs are all costs outside of the above costs:- Maintenance costs for machines, factories
- Amortization and depreciation (depreciation) costs of machinery and factory buildings
- Cost of water, electricity, factory gas
- Factory insurance costs
- Rental fees, and others.
Small and medium companies often make quite fatal mistakes, because when calculating production costs, they do not calculate the cost of space. For example, a coffee shop, because the place to open a cafe is your own, then you do not count this as an additional cost.
This results in, you see that your business is profitable, then you take the expansion step by opening a new location by renting a place. Often it is realized too late, after operating you feel your business is very good, sales are very busy, but you continue to lose money. Because your profits have been eroded by the cost of renting a place.
Production Cost Formulas
After looking at the existing components, the formula for the total Production Cost is as follows:
Production Costs = Direct Raw Material Costs – Direct Labor Costs – Factory Overhead Costs
Example of Calculating Production Costs
“Emphuk” is a bakery company, wherein 1 month the company can make 300,000 loaves of bread. Or 10,000 loaves of bread per day.
The following is a breakdown of the cost of producing bread each month:
- IDR 300,000,000 for flour, cheese, chocolate.
- IDR 100,000,000 for direct employee costs, from stirring, shaping, roasting, and packaging.
- IDR 50,000,000 for electricity, gas, machine depreciation, rental space.
The total production cost bread becomes: IDR 300,000,000 + IDR 100,000,000 + IDR 50,000,000 = IDR 450,000,000
And the production cost for 1 piece of bread is IDR 450,000,000 / 300,000 pieces = IDR 1,500.
So it is clear, by precisely calculating the cost of production, you can determine the selling price more easily. This total Production Cost also serves as the basis for calculating the Cost of Goods Sold.
Read also: What is the Cost of Goods Sold (COGS) and How to Calculate COGS
Production costs affect the cost of goods sold of a company’s product. Accuracy in the calculation of production costs is necessary so that price errors do not occur and result in company losses because they sell at a low price so that they lose or, on the contrary, sell too expensive so that the goods do not sell.
Use the IREAP POS PRO android cashier application. To help you calculate production costs in your coffee shop and restaurant, with IREAP POS PRO, the cost of raw material can be calculated immediately when you make a sale. So that your raw material and stock costs can be easily monitored for only IDR 40 thousand a month.