To carry out production and turn the wheels of the company so that it continues to grow, companies need to produce a product/service. For that, it takes several funds, known as production costs.
Production costs must be carefully calculated based on various components, such as fixed costs, variable costs, total costs, etc. Let’s read a full explanation of what production costs and their parts are in this article.
What is Production Cost?
The definition of production costs is the fund’s companies spend to produce goods/services, from processing raw materials to becoming finished goods ready to be sold to bring profits to the company.
Why is it important to calculate production costs?
Knowing how much the nominal cost comes out during the production process will prevent you from possible losses.
This is because production costs will later become a reference when setting the selling price. In full, here are the reasons why you need to calculate production costs, including:
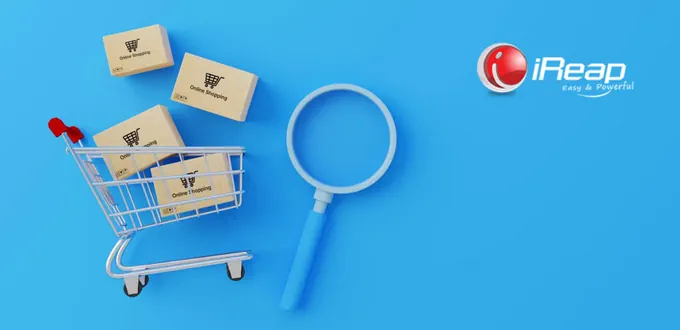
- Calculating production costs is an important aspect of preparing financial reports.
- To prevent business owners from experiencing losses due to runaway costs.
- Helping companies to evaluate profit and loss, as well as preventing fraud.
- Assisting the procurement department in selecting and establishing cooperation with suppliers.
- Help determine the right selling price.
- Product evaluation and improve the quality of raw materials.
- Efficiency in the production process and can be a source of relevant data for future decision-making.
Components of Production Costs
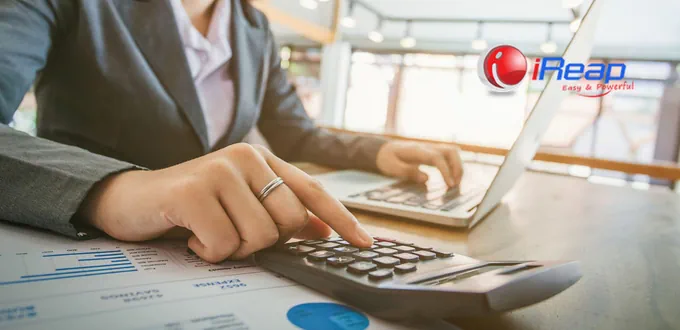
1. Direct Material Cost
Direct material or direct material costs are raw material costs that are directly related to production activities to produce products.
Later, these raw materials will be processed to become products with exchange value. You can immediately find out the nominal cost.
For example, in a coffee shop, direct raw materials are coffee beans, milk, sugar, water, ice cubes, and other ingredients directly used in making coffee drinks.
Another example is a bakery that requires raw materials, such as flour, eggs, milk, chocolate, cheese, butter, oil and others, to produce coffee products.
2. Direct Labor Cost
Direct Labor or direct labour costs are wages, salaries, benefits, bonuses, and even insurance paid to employees and are directly related to the production process.
For example, the salary of coffee shop employees (based on the example in the previous point), the wages of coffee bean-picking workers who work on coffee plantations, the compensation of employees who operate production machines, and so on.
Another example is an employee at a bakery who gets a wage because his duties are directly related to producing bread, from making dough and baking to packaging the finished bread.
3. Factory Overhead Cost (BOP)
Manufacturing overhead or factory overhead costs (BOP) are company expenses that have absolutely nothing to do with production activities in factories or in production activities that produce finished products.
There are three types of costs included in factory overhead costs, namely:
- Indirect or indirect material costs are all costs for using certain materials in the production process. Still, it is difficult to determine the nominal value for each product. For example, the cost of oil for frying, the cost of cleaning fluids to clean factories and machines, the cost of buying plastic packaging, and so on.
- Indirect or indirect costs are costs that are completely unrelated to the production process, but their role remains in the factory. For example, security guards (security guards), quality control departments, factory supervisors, and so on.
- Other factory overhead costs, such as factory leases, land leases, amortization and depreciation (depreciation) of factory machinery and buildings, factory safety insurance, factory utilities (water, electricity, gas), and so on.
4. Fixed Costs
Fixed or fixed costs are expenses for a period whose nominal value is set and does not depend on production results—examples: building rental fees, management fees, corporate taxes, administration, and others.
5. Variable Cost
Variable or variable costs are costs whose nominal value is not fixed/changes based on production results. The higher the output, the greater the variable costs you have to spend.
Conversely, if the production output is low, the nominal cost will be more minor. Examples of variable costs include the cost of raw materials used, packaging costs, and wages for workers based on the number of hours worked or the amount of production.
6. Total Cost
Total cost is the sum of all the fixed and variable costs used to produce the finished product over a certain period.
That is the calculation of total costs by adding fixed and variable costs.
7. Average Cost
The average cost is the expenditure of the production cost per unit. The average price is calculated by dividing the total cost by the number of products produced.
8. Marginal Cost
Marginal cost is the additional cost required to produce one finished good. These costs generally arise because there is an increase in the number of goods delivered.
When calculating production costs, you need to track down the sources or factors that cause these costs to arise. In this way, you will be able to find the flow of money related to the company’s production activities in detail. To make it more straightforward why you need to calculate production costs, read Functions and Purpose of Calculating Production Costs.