Production costs are expenses incurred in the production process or in the company’s efforts to sell finished goods. In calculating production costs, you need to pay attention to 3 types of production costs: raw material, labor, and overhead. Let’s look at the full explanation in this iReap article, including an example of calculating production costs.
Definition of Production Cost
The definition of production costs are all costs incurred when the company carries out the production process.
You should record all these costs and include them in the company’s financial statements so that later you will know how much it costs the company to produce finished goods.
Then compare the expenditure of all costs and profits derived from sales to determine whether the company is making a profit or is even experiencing a loss.
3 Types of Production Costs
So, for the calculation of production costs to be detailed and accurate, the recording must be by the types of production costs, namely:
1. Raw Material Cost
Raw material costs are all costs associated with procuring raw materials to be processed into products/services that companies can sell to consumers. Raw material costs are divided into two, direct and indirect raw material costs.
- Direct raw material costs are all costs to purchase raw materials that are in direct contact with the production process. For example, you can see the production process at a food depot. Direct raw materials, among others: vegetables, rice, fish, eggs, and other materials that are directly used in making various types of food.
Another example you can see it in the cake shop. Then what is included in the cost of direct materials, among others, is the purchase of eggs, refined sugar, butter, oil, wheat flour, cocoa powder, and others. - Indirect raw material costs are the costs of purchasing raw materials that are completely unrelated to making a finished product. For example, plastic wrap, glue, laundry soap for washing cooking utensils, greaseproof paper, and even raw material storage costs (electricity for refrigerators, pen ink for keeping records of raw material supplies, and others).
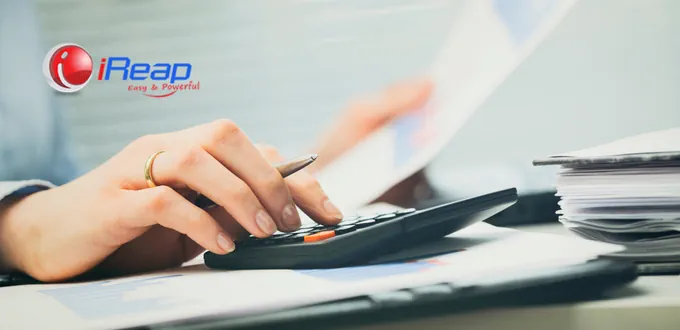
2. Labor Costs
Labor costs are costs related to labor in the production process. Just like the cost of raw materials, this cost is divided into two: direct labor costs and indirect labor costs.
- Direct labor costs are costs/expenses for paying the salaries/wages of workers directly involved in the production process, from raw materials to finished goods. For example, wages for coffee shop employees, employees who work to assemble products in a manufacturing company, or wages for production machine operators. The payment can be in the form of a weekly or monthly salary, or it can also be a payment of wages per project.
- Indirect labor costs are labor costs that are not at all directly related to the production process. For example salary for quality control, daily wages for production supervisors, salary for factory security officers, and so on.
3. Overhead Costs
Overhead costs are company costs or expenses that are not directly related to the production process but are still associated with situations or conditions that determine the smooth running of the company in producing goods.
Examples of overhead costs that you must take into account properly include:
- Rent a factory, warehouse, or place where the company produces goods.
- Cost of building arrangement (if the place of business is not a rental system).
- Costs for maintenance, maintenance, repair, and depreciation of production machines.
- Costs associated with the use of electricity, water, telephone, gas, or other fuels.
- Factory insurance fees, security system fees, and so on.
4. Marginal Cost
Marginal costs are additional costs or expenditures that companies need to make to increase production, for example, to increase the number of finished goods due to high market demand.
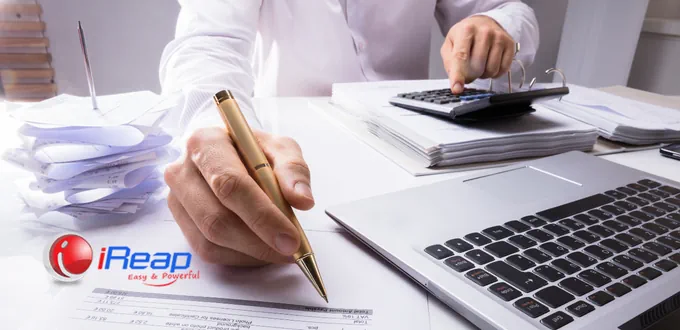
Be careful! These Costs Are Not Included as Production Costs
Often what happens, business owners unknowingly include several other costs, which are indeed related to the production process but are not included as production costs. For example, advertising costs and distribution costs.
- Advertising costs are costs for promoting products/services with the aim that more and more consumers are interested in purchasing. This advertising fee is included in marketing costs.
- Distribution costs are costs associated with the distribution of goods/services so that consumers can easily find them. Distribution costs can be in the form of transportation costs, toll road rates, vehicle maintenance costs, etc. Even though it looks related to finished goods, this cost still needs to be included in production costs.
Example of Calculating Production Costs
To calculate production costs, you need to use the following formula:
Production costs = raw material costs + labor costs + overhead costs
If the business you are running is related to bread production, for example, then the production cost calculation for 5000 packs of bread is:
- Cost of raw materials: IDR 5,000,000,-
- Labor fee: Rp. 10,000,000,-
- Overhead costs (factory rent): Rp. 3.500.000,-
Then the total production cost to produce 5000 packs of bread = IDR 18,500,000
To prevent losses in running a business, you must calculate production costs carefully, including paying attention to expenses according to the type of production costs. In this article, you will also find examples of calculating production costs. So, to understand more about the complete formula and how to calculate, learn: Formulas and How to Calculate Production Costs.